Iron Industry
Iron
Why Iron Was Important:
Tools, cooking pots, hardware, nails, farm implements, and many other essential everyday items were made of iron.
Design of the Iron Furnace:
Iron was smelted in a stone or brick furnace 25 to 28 feet tall and about 24 feet square at the base. If possible, iron furnaces were built near ore deposits and next to a strong flowing water source. The water power was utilized to operate a massive bellows that blew a constant stream of air into the base of the working furnace. The air increased the temperature within the furnace and was essential for successful smelting.
Process:
The iron ore used in local furnaces was a coarse, dark brown sandstone frequently seen in Virginia and Maryland; it was also called bog ore. The ore was dug from shallow pits and, using a sledge hammer, broken into walnut-sized pieces. Charcoal served as fuel and oyster shells acted as a flux to remove impurities from the molten metal. Once a fire was started in the furnace, operators attempted to keep it going, 24 hours a day, 7 days a week, for 6 to 9 months at a time. Measured quantities of ore, charcoal, and oyster shell were added to the furnace every few minutes. A temperature of about 1400 degrees Centigrade was necessary for optimal smelting.
There were several holes at the base of the furnace that could be tapped open allowing the molten iron to flow into shallow molds formed in a bed of sand next to the furnace. Once cooled, these “pigs” were broken apart and were then ready to be made into functional articles.
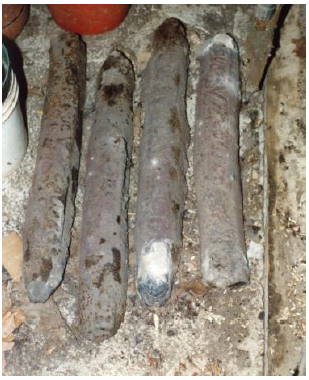
Also tapped from the furnace was a molten glassy substance called slag. This was the silica or quartz that made up a large percentage of the bog ore. The slag was tapped out into the sand pit and allowed to cool. Once hardened, this waste material was broken up and carted away.
Forging:
Iron straight from a furnace is called cast iron. This could be used for cooking pots but was too brittle for most tools, nails, or other iron items. To make stronger iron articles such as tools, hardware, etc. the cast pigs had to be processed in a forge. The iron was heated until malleable, then hammered to force out impurities. After sufficient processing, the iron could be hammered into axes, hinges, nails, knives, or any other necessary item. Despite the naming of Colonial Forge High School, there was never a forge at Accokeek. Principio’s forges were located in Maryland and the Accokeek pigs were hauled by ox cart from the furnace to Coal Landing on Aquia Creek, then carried by ship to the Maryland forges or shipped directly to England.
Accokeek Iron Works:
During the 18th century, Stafford was home to two major ironworks, Accokeek and Hunter’s. Accokeek Iron Works operated from c.1725 to c.1752 and was located on Accokeek Run not far from Colonial Forge High School. Owned and built by the Principio Iron Company of England, it was one of the earliest and largest such facilities in the Chesapeake region. Augustine Washington (1694-1743), father of George Washington, was a major stock holder in the company and until the early 1750s Accokeek was the headquarters for the Principio Company.
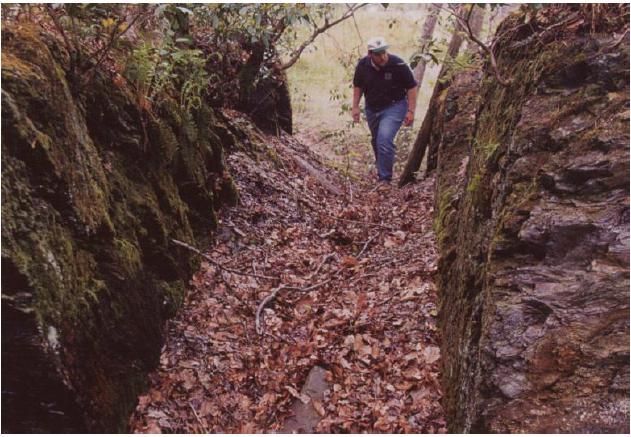
James Hunter’s Iron Works/Rappahannock Forge:
This facility operated from c.1759 to c.1810. It was established and owned by James Hunter and stood on the Rappahannock River just north of Falmouth. Hunter had a canal dug to channel river water to his mills. This was ¾ of a mile in length and began just below the present northbound bridge of I-95. To ensure that flood waters didn’t damage his valuable mills, he had massive gates built at the canal entrance. These could be closed in the event of flooding.
At Hunter’s Works were made all manner of tools, nails, chains, and other hardware. Rappahannock Forge was the gun making division of the iron works and was not established until about 1776. During the American Revolution, this facility was a major producer of tools, supplies, and weapons for the Continental army and navy. These included entrenching tools, pistols, rifles, amusettes (a cross between a shoulder-arm and small cannon), carbines, muskets, chain, anchors, bullet molds, nails, camp kettles, canteens, horseshoes, etc. A number of Hunter’s firearms survive and are highly prized by collectors.
Hunter’s was a massive multi-faceted manufacturing center and was one of the largest such operations in colonial America. Shops on the site included an iron furnace, brass furnace, flour mill, wire mill, saw mill, gunsmiths’ shop, anchor shop, still, forge, just a partial list. In 1770 a British customs officer reported that Hunter’s was the largest iron works upon the Continent. Prior to the Revolution, Hunter obtained some of his iron ore locally and some from Maryland. In 1776 Hunter was allowed to take over the old Accokeek mines because British warships made it too dangerous to ship ore from Maryland.
The operation employed hundreds of people, both Black and White, enslaved and free. Housing would have created a village that most likely stood on both sides of the I-95/U. S. Rt. 17 interchange.
James Hunter (1721-1784) was born in Glasgow, Scotland and was a merchant. He and his brother, Adam Hunter (1739-1798), also ran a store in Fredericksburg. James lived at Stanstead, which was located where the new Target stands near the I-95/Rt. 17 interchange.
After James Hunter’s death in 1784, business at his works severely declined. Virginia was bankrupt and unable to pay its bills, including a substantial amount due Hunter’s estate. After the close of the Revolution, a general economic depression overtook the area. Hunter’s administrator revitalized the blacksmith’s shop and forge and continued to operate those for several more years. Most business ceased there around 1810, though some years later one of the old mills was converted first to a commercial flour mill and then to textiles.
Sources:
- Eby, Jerrilynn. Laying the Hoe: a century of Iron Manufacturing in Stafford County Virginia. Westminster, MD: Willow Bend Books, 2003.
- Lewis, Ronald L. Coal, Iron, and Slaves: Industrial Slavery in Maryland and Virginia, 1715-1865. Westport, CT: Greenwood Press, 1979.
- MacMasters, Thomas E. The History and Technology of Governor Spotswood’s Iron Furnaces in Spotsylvania County, Virginia, 1721-1792. Los Angeles, CA: University of California, 1974.
- Pearse, John B. A Concise History of the Iron Manufacture of the American Colonies up to the Revolution. NY: Burt Franklin, 1876.
- Robbins, Michael W. The Principio Company, Iron Making in Colonial Maryland 1781 NY: Garland Publishers, 1986.